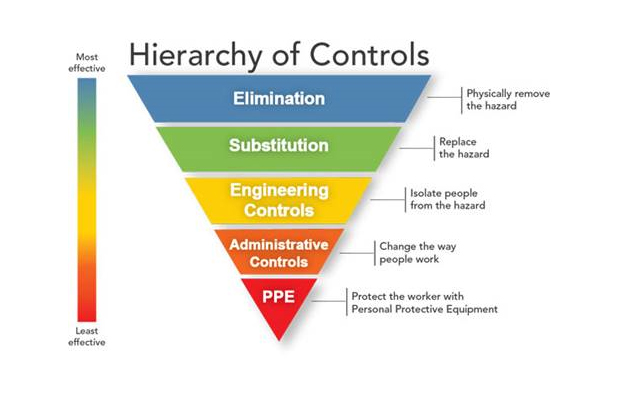
Having the mindset of eliminating a risk in a brewhouse setting is more important than finding a solution to work around the problem.
That’s how Highland Brewing’s Andrew Klosinski tackles the thought process for his brewery. Using a reverse pyramid figure called the “Hierarchy of Controls” the Brewing Operations Manager for the Asheville, North Carolina facility, said that elimination, followed by replacing the hazard, are the most important aspects of the brew team’s risk management in creating Standard Operating Procedures for each system in the brewery, be it in brewing, grain handling and storage, cellaring or cleaning.
“Our goal with this mindset is to eliminate the risk all together rather than just relying on SOPs and PPE to protect our team,” he told Brewer. “Our efforts to eliminate risk and engineer solutions for increased safety have definitely had a positive impact on the way we approach and develop SOPs for the brewhouse.”
Surly Brewing is always working on improvements to its SOPs, making it a living document.
“We have a monthly safety committee meeting led by a senior brewer that incorporates the leads of all of the production sub-departments, including brewing, packaging, warehouse, QA/QC, and maintenance,” explained Surly VP of Brewing Operations, Will Crosby.
Following the monthly safety meetings, trainings are held with each department so all team members know the updates or modifications to SOPs.
“We also continue to meet requirements for lift certification, TIPS training, and right-to-know training for chemicals,” he added.
Surly’s SOPs are revisited regularly by a committee that includes management, lead brewers, and shift brewers from each location, along with the lab manager.
“This committee meets on a weekly basis to look at one specific process SOP at a time and gather feedback,” Crosby said. “Any revisions that are made are logged in the master SOP document and then distributed to the entire brewing team. Training audits are also performed on a regular basis by department leads to verify that proper training has been completed and are being followed.”
Highland’s shift to the Hierarchy of Controls mindset with risk avoidance through engineered solutions that isolate, substitute, or, try to, eliminate the risk changed the way Klosinski and his whole team approached SOPs.
“One small, but effective example would be the replacement of the standard tri-clamp to a high-pressure/bolted clamps on high-temperature wort lines, hot liquor lines, and tank outlet valves,” he said. “We identified elevated risk connected to those areas, made the change, and the result has yielded three benefits – providing a solid, tamper-proof joint, serving as a constant reminder of the criticality of these connections, and a visual affirmation of Highland’s commitment to employee safety.”
Crosby noted that Surly has an extensive training schedule with all operators, and it takes an average of 12 months for a trainee to become a fully validated brewer on all brewhouse and cellar operations.
Here are three ways these breweries approach certain areas of its SOPs:
CIP
Surly has two separate automated CIP systems in its large brewery: one services the cellar, the other services the brewhouse.
“We follow normal brewhouse CIP protocols, including caustic CIP, acid CIP, and sanitization cycles of all equipment at prescribed intervals,” Crosby said. “We also have the ability with our automation to clean the hot and cold liquor systems, as well as our wort oxygenation unit. All CIPs are run on conductivity and validated with titration of chemicals. Rinse water samples are checked on the spot with ATP validation and samples are run in the lab to validate CIP’s as needed.
Klosinski added that Highland performs manual CIPs on all equipment, and it has a high degree of brewer involvement, which has its benefits.
“Having eight sets of eyes on a process will result in two important things: Questions being asked of the current SOP — the ‘why’ — and people learning from and refining the SOP — the how.’
Highland continues to move towards semi-automated CIPs over time but Klosinski said they remain cognizant of the benefits the human factor brings to continuous improvement efforts.
Grain storage & safety
Taking milling and malt handling SOPs very seriously needs to happen not only because of the obvious safety concerns but also for the important role those processes play in achieving the quality and integrity of the malt and ultimately the end product of delicious beer.
Recently, Highland completely overhauled its malt elevation automation.
“It was a good opportunity to review which SOPs were working and build in additional safety features to our process,” Klosinski said. “Particularly with improvements to milling and malt handling, taking the time to evaluate and improve safety protects a critical asset and provides safe conditions around the mill that have been shown to improve brewhouse extract yields.”
The majority of Surly’s base malts are in closed silos with a conveyance system to the mill. Crosby said they store all but the weekly usage of its bag malt and supersacks in an offsite warehouse. This warehouse contains grain storage, cold storage for all finished beer, packaging materials, and a barrel-aging warehouse. All areas have a separate section in the building.
“We are diligent about storing grain in our racks, inspecting on a weekly basis, and having an active pest control program with an outside partner to make sure that optimal storage conditions are met,” he said.
Insurance
Surly has also worked diligently with its insurance broker to help make sure that the facility is meeting current federal and state regulations for safety in manufacturing.
Typically an insurance company has broader safety initiatives that are helpful, but generally are a little less specific about individual brewery processes, pointed out Brock Ashburn, Highland’s Director of Operations.
“I highly recommend reviewing the insurance company safety documents and taking them up on offers to come and present safety initiatives,” he said. “They are well-written and always contain nuggets of info that help develop individual company safety culture.”
Be the first to comment