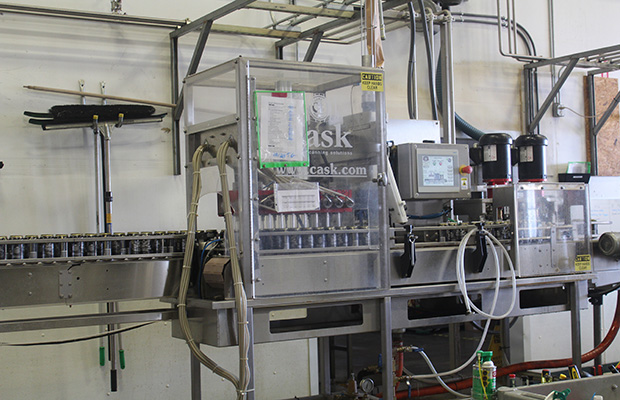
Preparing for what’s next is always on the mind of a brewery decision-maker. Sometimes a brewery gets the opportunity to plan and build a canning line in a new facility. But many times it seems that the need for your own line happens before that can happen. Brewer talked with breweries that have grown to output more than 15,000 barrels per year and have worked on adding canning lines in both senses.
For Ecliptic, the canning line didn’t show up until a couple years in and the brewery had grown exponentially, explained Packaging Manager Grant Smith.
He said the line is very centrally located in the brewery, directly across the aisle from the brew deck.
“There is a delicate ballet when mashing out and pallets of finished product are completed or new stacks of cans need to be loaded into the depal,” he said. “The real change came when we got our off-site warehouse up and running.”
Prior, finished pallets used to be stacked next to the loading dock, but now they are wrapped and loaded right onto a box truck and whisked away when the truck is full.
“This allowed us to keep more consumable inventory on hand (ends, cans, trays, Paktech handles, glass, etc.), and keep production moving,” Smith said.
Given the fairly unique nature of MadTree‘s production space, Packaging Manager Matt Duddey said they were allocated a certain space and had to make it work.
“During buildout, we worked with a packaging layout consulting company which likely saved us from ourselves,” he said. To maximize space the line double backs, putting the depalletizer (robot) next to the Switchback case packer.
“Our cooler is about 20 feet from the off-pack area so the whole layout is super compact,” Duddey said. “Some days the forklift reminds me of the scene in Austin Powers where he’s stuck in the hallway. Lots of forwards and backward with cans and kegs in a tiny footprint.”
New Realm‘s Mitch Steele said when they worked on the canning line for the Georgia brewery, they focused on a few things: proximity to bright tanks, ease of delivering and staging packaging material, drains, and easy flow from discharge of the line to the warehouse.
When Kentucky’s Braxton Brewing beefed up production, co-founder and CPO Evan Rouse said they worked directly with the manufacturers of the canning line and the conveyance to help design the layout, including the efficiencies of the layout.
“Our biggest hurdle was the very small footprint in which to fit in a rotary mono-bloc filler,” he said. “To do this, you will spend more on conveyance, but it is possible to get it into a tight footprint.”
Braxton made sure to be able to have a reflow accumulation table post-fill inspection and date coder, all before any of the ancillary equipment, such as a labeler or the PakTech applicator.
“We then designed the layout to make these items optional in the line — making them easy to remove if they are unneeded for that run,” Rouse said. “We then utilize a pallet positioner for manual palletizing of product that is already in case trays.”
Smith said that Ecliptic packages beer six days a week and the most important thing they can do to set ourselves up for success is to make sure the beer is presented properly and verify the presentation before running.
“If the beer is 45 degrees and carbed to 2.9 vol. of CO2, you’re going to have a pretty bad day on the line,” he said. “We had to work with the brewers to present the product for packaging, while still carbed for style and minimal DO pick up.
“We are fortunate enough to have an Anton Paar CBox to verify the product is carbed properly. The packaging team runs the CBox before hooking up to the tank, so they know what they are getting into.”
Ecliptic’s spec is 2.5-2.7 vol CO2 and 32 degrees at the tank.
Other than making sure the beer is in spec, keeping up on scheduled maintenance is key.
“It minimizes downtime during a run and keeps your equipment running longer, better, and faster,” Smith said. “A robust spare parts kit doesn’t hurt either.”
Photo courtesy Iron Horse Brewing
Be the first to comment