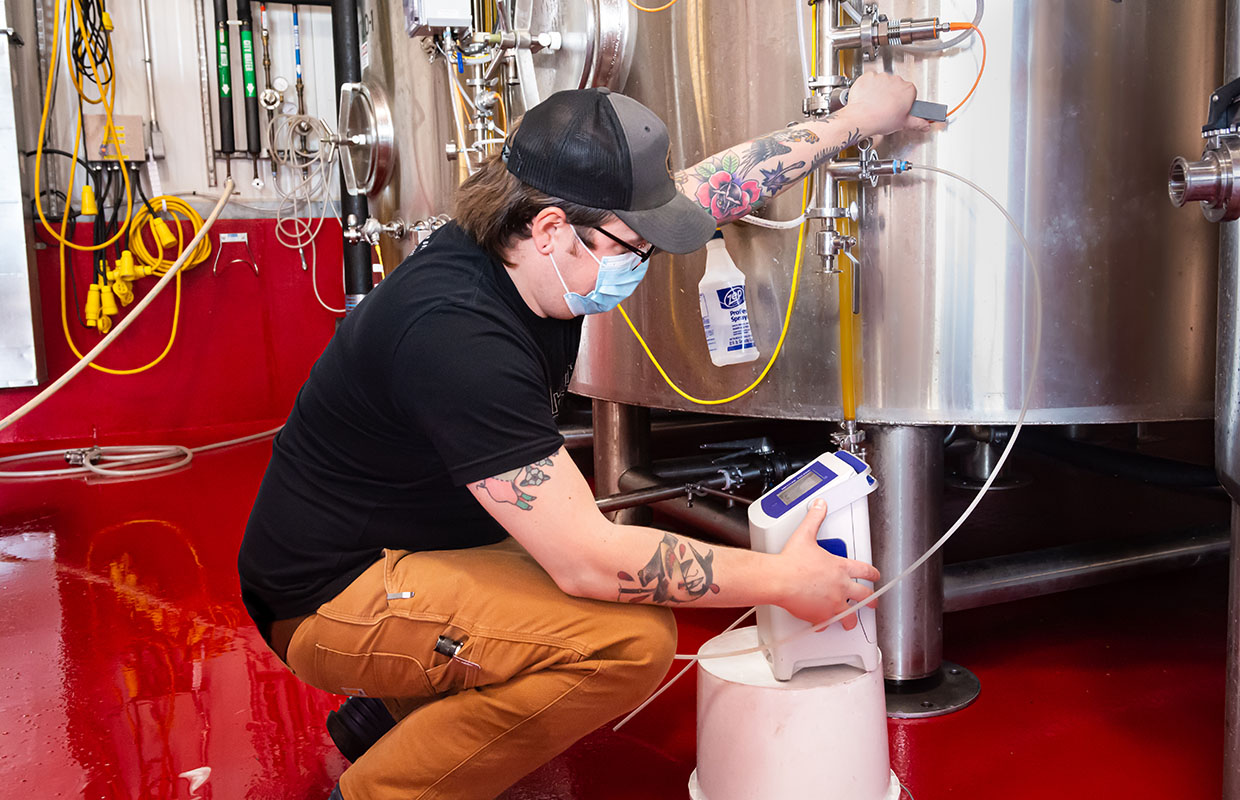
Oxygen is not a brewer’s friend, or a packaging manager’s … or even the end consumer’s. Freshness counts and it can translate to repeat sales, so getting it right at the start and preventing oxidation during carbing is a paramount to ensuring quality.
Identifying problems and solving them are a natural progression of growth for many breweries and sharing those strategies can help boost the entire industry.
Carbonation Strategies
Topa Topa Special Operations Brewer Joseph Isaac said that the California brewery works at cutting down on carbonation times by ensuring that they maintain a constant head pressure on capped fermenters (with daily pressurizations to maintain one bar of CO2 pressure).
“This naturally carbonates the beer prior to transferring to a brite beer tank, which helps cut down the total carbonation time post-transfer,” he said. “If we ever do transfer beer and find the oxygen levels are too high, we’ll burp or scrub the tank of oxygen prior to carbonating.
To do that, they will gently bleed out all head pressure and push carbon dioxide into the bottom of the tank — but not through a carb stone — at a higher pressure like 30-40 psi until measurements show oxygen levels are to specifications.
“This will reduce carbonation as well, but… started from the bottom, now it’s beer,” Isaac points out.
The biggest issue Bent Water comes across is a carb stone not dispersing CO2 into the beer.
“Usually this happens on very turbid beers and is caused by clogged pores,” said Director of Quality Adam Denny Golab. “To mitigate this problem, we put a second stone in our brite tanks that can be used in the event of a carb stone failure.
Changing the frequency of our CO2 measurements of carbonating beer has also helped identify carbonation problems before they impact Bent Water’s packaging schedule.
“Having multiple people with eyes on a carbonating tank has reduced the opportunity for delays to occur,” Denny Golab said.
Beer temperature can always be an issue when carbing but having clear specs for cold beer when centrifuging and allowing ample time for carbonation before packaging solves most of these issues.
Occasionally a hazier beer can cause issues with carb stones but proper cleaning and maintenance of these will prevent most issues explained Surly’s VP of Brewing Operations, Will Crosby.
The Minneapolis brewery has different systems at each of its breweries for carbonation. At the larger production facility, they have a Pentair carbonation skid on the outfeed of its centrifuge to carb in-line [see inset].
“Since it’s a closed system, the most critical input is CO2 purity,” Crosby said. “We evaporate from our bulk tanks and see a good level of purity; we also monitor DO in-line when carbing to ensure that we don’t fall out of spec.”
At the original location, a smaller brewery, Surly has carb stones in the bright tanks.
“These are cleaned and purged between uses, and once filled with centrifuged beer we carb via carb stones from our CO2 skid,” Crosby said. “Maintaining proper head pressure and carbing gently allows us to dial in the desired level and maintain good O2 levels. These are monitored throughout the process with a c-DGM Gehaltemeter.”
The biggest problems for Braxton Brewing in the process was the length of time it took to complete carbonation as well as the inconsistent readings from its Zahm & Nagel CO2 measuring device.
“Once we upgraded to a pin-point carbonation device and the Anton Paar C-Box, both the speed of the carbonation and the accuracy of the carbonation measurement were faster and more reliable,” said co-founder and CPO Evan Rouse.
He explained that after CIP in the brite tanks, the brew team will fully purge the tank to eliminate any oxygen in the tank head space. From there, they utilize the pin-point carbonator as well as a ceramic carbonation stone in brite tanks during the carbonation process.
Topa Topa monitors oxygen levels as the batch moves through the cellar, including purging the transfer pathway, tightening clamps after they cool down and contract, creating a CO2 blanket during dry hop and such
Lead Brewer, Justin Clemente noted that they also monitor oxygen levels during carbonation with an Anton Paar C-Box.
“It’s also important to use dedicated CO2 lines (and to be kept closed when not in use) that are never used for anything but CO2,” Clemente said. “Carbonating while the tank is at the proper head pressure will also help prevent oxidation.
“One more important step is to properly purge your brite beer tank prior to transfer to ensure that there is a low-to-zero-oxygen environment to welcome the beer; we purge the tank to oxygen levels of less than 50 ppb.“
One of the biggest changes Bent Water made in the past year was to purchase a Mettler Toledo InTap oDO Analyzer to validate brite tank purges.
“Previously, the sniff test was our method to determine if our brites were purged,” Denny Golab said, adding this was not only subjective, but it wasted a lot of time and CO2.
“The Intap has allowed us to make sure that brite tanks have been completely purged of oxygen and that it is consistent from operator to operator,” he said. “This has allowed us to achieve more consistent low DOs in our cans.“
Carb Stone Utilization
Topa Topa will clean, sanitize with 180°F water from the hot liquor for five minutes, and purge carb stones prior to every use. Brewmaster Casey Harris explained that after packaging off the brite tank, they’ll use sanitary water to flush out the carb stone and then use carbon dioxide to purge it prior to storage, where they are kept vertical on a rack without anything contacting the carb stone surface.
“Don’t touch the carb stone with your bare hands or set it down on any surfaces,” he said. “We have one-piece carb stones, so no disassembly is required. If you can disassemble your carb stone, we’d recommend breaking it down every time and using caustic and peracetic acid cycles since those carb stones are prime places for the growth and flourishing of bacteria. Nobody likes a dirty carb stone.”
With the use of an in-line pin-point carbonator Braxton beer is leaving the centrifuge and running through a glycol heat exchanger and into the pinpoint. So Rouse said the beer is entering the brite tank at or just below full carbonation.
“Once the separation is complete, we will take a CO2 and DO reading and make any fine tune adjustments with the carb stone to hit our target co2 volume,” he said.
Braxton leaves the carbonation stones in the tank during a CIP and pulls them to sit in a caustic soak, fully disassembled. The carbonation stones get cleaned each time the tank gets cleaned, as well as inspected for any broken gaskets or issues with pores in the carb stone.
Between uses, Surly makes sure to disassemble and clean the carb stones — particularly the check valves that are present and the stone itself — to be sure that they will perform correctly.
Denny Golan said carb stones are blown out with CO2 and soaked in caustic. They are disassembled and HLT is run backward through the stone to flush the pores.
“After reassembly the stones are blown out with CO2, sanitized with PAA, and blown out again,” he said. “Periodically they see acid to deal with any inorganic matter and are put in a caustic sonic cleaner bath to shake loose any “hangers-on” to keep those pores clear.
“It’s shocking how much can come out of a stone when it gets in the sonic cleaner.“
Surly has some ceramic carb stones that require special care, Crosby said.
“They need to be removed from bright tanks as soon as possible after use to avoid beer drying on them,” he said. “They’re soaked in water until full cleaning, which entails flushing through with water and then gas. There is a specific pyrophosphate caustic blend that is recommended by the manufacturer to clean these and it does a good job removing organic material after soaking.
“They are then placed back in the tank for normal CIP and sanitation protocols prior to purging the tank.“
Crosby added that stainless carb stones are more robust and can be cleaned well with caustic and normal flushing. They make sure to have minimum 15-20 psi head pressure on the tank to be carbed and then run CO2 through the carb stone at 25-30 psi.
Ditching the Carb Stone: Insights to Inline Carbonation Systems
Inline carbonation is another solution to oxidation issues and ProBrew specializes in helping breweries eliminate the extra work it takes to keep a carb stone clean.
“When we first got into the craft beer industry, we saw right away the benefits of inline carbonation over traditional brite tank stone carbonation,” said Derek Deubel, ProBrew President. “First, inline saves an incredible amount of time — you can carbonate 20 bbls in less than an hour versus waiting an entire day or more for carb stones to do their thing, and that’s just with our smallest unit, the ProCarb MINI.”
With inline carbonation a brewery team member can easily control the exact volume of carbonation they want to inject into the beer using the meter-based PLC controls to adjust flow rates and ratios.
“That, in combination with how much carbonation was naturally produced during fermentation, you can hit the perfect volume every time while evenly distributing the gases throughout the beer,” Deubel said.
ProCarb uses cost-effective, meter-based PLC controls for consistently accurate carbonation volumes and processing speeds. ProBrew offers ProCarb inline technology in speeds ranging from five gallons per minute with the MINI up to 230 gallons per minute. All ProCarb systems can go directly to cellar tanks or packaging with exception of the MINI that goes straight to packaging.
ProBrew’s line of ProCarbTM Inline Carbonation systems prevent oxidation because the beer or other beverages are never exposed to the air — one of the many benefits of inline, said ProBrew Marketing Manager, Roxanne Gorham. “The only time the beer would start to pick up oxygen or lose carbonation would be at packaging, especially with an inline, open-air filler. We actually manufacture the ProFill Can filler — a rotary, true-counter-pressure-gravity can filler that purges the can of oxygen before filling — to further reduce DO (Dissolved Oxygen) pickup and loss of carbonation at the final stages of production.”
The ProCarb systems quickly send beer from fermentation, Deubel said, through the ProCarb and can go right into packaging.
“A lot of guys brewing in smaller facilities appreciate the amount of space they save with the ProCarb because they can eliminate additional tanks and move product through faster,” he noted.
In 2016, ProBrew Technical Director, Peter Schultz also played around with carbonation and centrifugal technology at a Chicago brewery. Using a centrifuge was nothing new but Schultz decided to reverse the process and carbonate first.
By using the ProCarb to inject CO2 upstream of the centrifuge, they found that gases like CO2 and Nitrogen absorb better into the beer — and stay there.
“We actually filed for – and received – a patent on that technology that we aptly named the ProCarb Plus,” Deubel said.
Be the first to comment