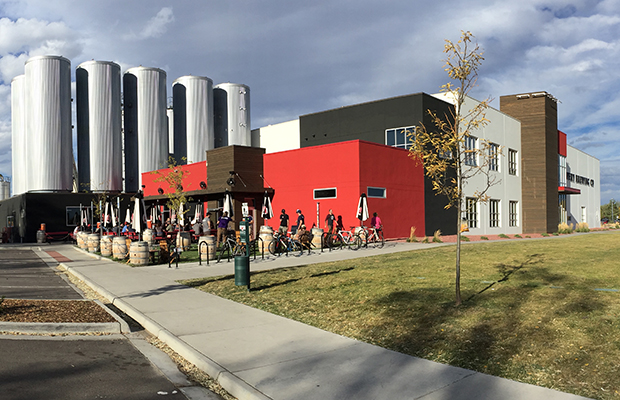
Opening in 2015, Avery Brewing‘s Adam Avery was proud of finally having a “showpiece” brewery. Spending $90,000 on its first brewhouse in “the alley” — a mix of three buildings that pumped out beer for the brewery over more than 20 years — the new Avery location was at a cost of $30 million. Creating that brewery took a lot of failure on Avery’s part, meaning that Adam Avery said he learned a lot from previous buildouts at the former location.
“We already had an amalgamation of like three different building types,” he told Brewer in a recent interview. “We had pipes going everywhere … and retrofitted things. And we looked down that road, we looked at some buildings. Obviously, the cost of retrofitting those buildings would’ve been a lot less than building a new facility. But in the end, it would just be where we were before, a warehouse repurposed into a brewery instead of having a world-class brewing facility so we can make a world-class beer.”
Now, Avery believes that the first facility made great beer back in the alley, but the beer the Boulder, Colorado brewery now makes it so much better.
“It was about beer quality is what it came down to and making it in a super, super safe manner,” Avery said. “A brewery that is built to be clean is easier to keep clean.”
Avery said he knew how not to do something because “you can go to the alley and see what not to do.
“We were thinking about how to do the exact opposite. We were in that facility for 20 plus years. You know the inefficiencies, you know what you are going to get.”
Where they came from became a checklist of what Avery wanted in the brewery.
“For me, a linear flow was key. There’s beer flowing from the one point in a linear fashion all the way to packaging and out the door,” he said. “A very, very simple thing.”
And planning for the future was key as well. Having the room to grow, if needed, was a component of the construction also.
“We were figuring out how to maximize that 5.6-acre footprint,” he said. “We know we have a gameplan for growth and how we grow out tank farms and how we add brewing vessels and such.
“I have smart guys that I work with that are my teammates.”
That group is a 6-10 person fold from different departments to talk about growth and how Avery as a company looks at facilities.
Avery didn’t get everything he dreamed of though.
“[You design] the building and then all the costs come in and you are like HOLY CRAP,” he said. “The building was much more grandiose in my mind in the way we originally intended the building. So we really kind of hacked things down to a smaller space. And in the end, I’m glad it happened that way.”
Putting dollars into equipment over other aspects was the first change
“If we had more building we might not have as big of a canning line, for instance, or even hiring some of the employees that we have now,” he said. “I really think we put in a lot of time to design and develop the building.”
Be the first to comment