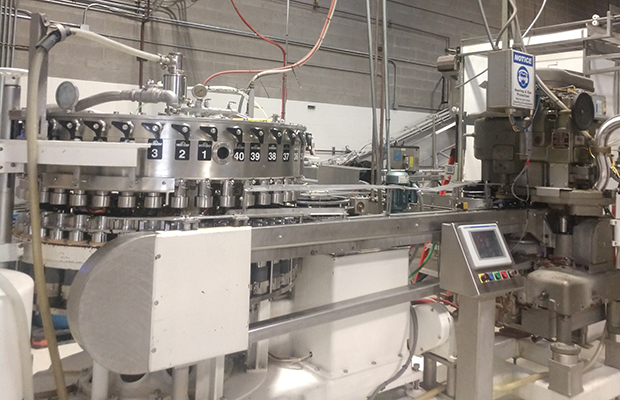
In an ongoing series, Brewer will take a small note from interviews of some of the Fundamental stories it has run in print and give a small tidbit that didn’t make the issue but is still worth diving into. “Decisions to Ponder When Upping Canning Load” appears in the September/October issue of Brewer.
When compiling information for a Brewer Magazine Fundamentals piece, sometimes it’s like pulling teeth, and sometimes it’s a waterfall of information sent back to you. In cases like that latter, I find that it’s all worth sifting through and sharing. Everyone’s experience can be shared and others can learn something from it.
Usually, a good-sized story that runs in Brewer may have three or four breweries featured. When it came to chatting about canning lines, we heard back from almost a dozen. Of course, each brewery has its own methods, so instead of trying to tie all these responses into a neat package, here are 10 thoughts on repairs shared by brewery members and those that create and work on canning lines. We hope you can get some inspiration and maybe even an ‘a-ha!’ moment that will send you to double-checking something on your canning line today.
The question posed that elicited these responses was: “What do you find is the most difficult repair on your canning line and what are your tips on preventative maintenance?”
- Martin Bills — Pelican Brewing, Director of Brewing Ops: The cartoner is a consistent issue. There are some issues of material performance of the cartons themselves, but even seasonally they’re fairly minor. In our case, we didn’t make the best choice for the cartoner manufacturer. Performance on 12oz cans is acceptable. Performance on 19.2oz cans is a circus. It has taken months for our expert packaging teams to quickly change over this equipment. Our folks are sharp, agile , and dedicated to the process. There are many moving parts in a cartoner. Regular cleaning and maintenance are essential. Get the sticky beer off. Tighten the nuts and bolts that routinely loosen or fall off. And buy the ’right’ equipment at the start.
- Jeff Martin — Great Divide Brewing, Packaging Manager: My experience is that the most difficult fixes are the ones you are not prepared to fix. Most new equipment will run without much maintenance but as time progresses and wear and tear begin to affect your line equipment failure is inevitable. Working with your equipment suppliers to have spare parts on hand is vital to keeping a line running. My biggest advice for PM is to work with your techs. They run the equipment daily and properly training packaging technicians to complete preventative maintenance goes a long way to finding and fixing small issues before they cause your line to shut down. I have also found this helps packaging technicians with training as they better understand the working of each machine
- Dan Ciaglo — Deschutes Brewery, Packing and Warehouse Manager: We’ve spent a lot of time working on our seamer, it’s a very precise piece of equipment. We have seen some equipment failures, but have also learned how slight can variations can cause immediate issues. We’ve learned a lot about seaming through issue resolution. Training for the seamer adjustments, timing, and repair is a must, as it is a pretty intimidating piece of equipment.
- Mike Wayne — Boomstick Brewing, Brewmaster: It’s all pretty straight forward on packaging lines. You have a combination of the five simple machines and when wear happens you replace the one(s) needing attention. It’s amazing to me how sensitive these lines can be. Sometimes as little as .002” is enough to cause issues with transition tables, or lift cylinders, or can end hooking. Learning how to watch a canning line takes time and if you’re constantly reacting to each instance you’ll never learn the whole operation. Sometimes you have to let the machine fail so you can learn and make the needed adjustment.
- Grant Smith — Ecliptic Brewing, Packaging Manager: Our CB-100, PSA has actually done a pretty good job of keeping the commonly replaced items relatively accessible. There is still a fair amount of disassembly to replace index cylinders. But it is a very solid design and much easier to wrench on than some other lines I’ve worked with.
- Jaime Oquendo — NOLA Brewing, Intoxicologist/Director of Facilities & Quality Assurance: The most difficult thing to fix would be the bearing blocks that control the cams for each of the seamer arms. When either of those fail, the cans won’t seam properly, so when you replace it you have to adjust it to the correct position to get the cans’ seams back to appropriate specifications. This requires a lot of minor adjustments followed by a seam width check after each adjustment. Sometimes that goes really smoothly, but when it doesn’t it could take an entire workday. As for preventative maintenance, keep anything on your canning line that has a grease fitting well lubricated (seam rollers, conveyor parts, etc.), and cleanliness. Cleanliness is probably the top item that will keep your canning line running for years.
- Gabe Wilson— SanTan Brewing, Head Brewer: We had a gear break that drove the infeed conveyor. We ended up discovering a previously unknown grease point that had never gotten greased. All grease points must be known and they are greased daily. If any of those fail, your entire line goes down until it can be repaired.
- Evan Rouse — Braxton Brewing, co-founder/CPO: The most difficult item to repair on the canning line has been the individual filling cups. They are made up of several internal parts and were delivered to us out of spec. CFT had an engineer on site within a few days and helped rectify the situation. Other than that, as long as you follow your manufacturer’s PM guidelines and stay up to date with these types of items, they tend to run like a well-oiled machine with very little issue.
- David Racino — American Canning, co-founder/CEO: Because canning lines require a wide variety of repairs over time, choosing equipment that is easy to understand and work on is essential. The number of custom components incorporated into a machine may cause sourcing replacement parts to be inordinately costly and/or time consuming. For this reason, breweries should always stock spare parts for critical components such as sensors and bearings. There is nothing more frustrating than losing two days of production to a $12 sensor. Performing routine preventative maintenance is key to keeping any line running smoothly, especially filler/seamers. If you don’t take care of your equipment, issues tend to compound and you may experience a series of cascading failures. Simple tasks like daily cleaning and greasing bearings can greatly help cut down on the frequency of component failures.
- Michael Stout — Craft Canning: As a mobile canning company, the most difficult repairs for us are the ones needed to be done over the phone when our equipment is packaging products hours away from our headquarters. Situations like these are where thorough staff training with all equipment instills confidence in our crews to successfully make a repair in the field with readily available support from our machine/QC team remotely. We do weekly check-ins on all of our equipment that addresses any issues that arise and preventative maintenance keeps our equipment in top shape. We do additional seam analysis to support our standard field protocols to ensure the best packaged product for our clients. Based on all of the information and data we are continually collecting, we schedule downtime for equipment needing a deeper dive by our maintenance team.
1 Trackback / Pingback