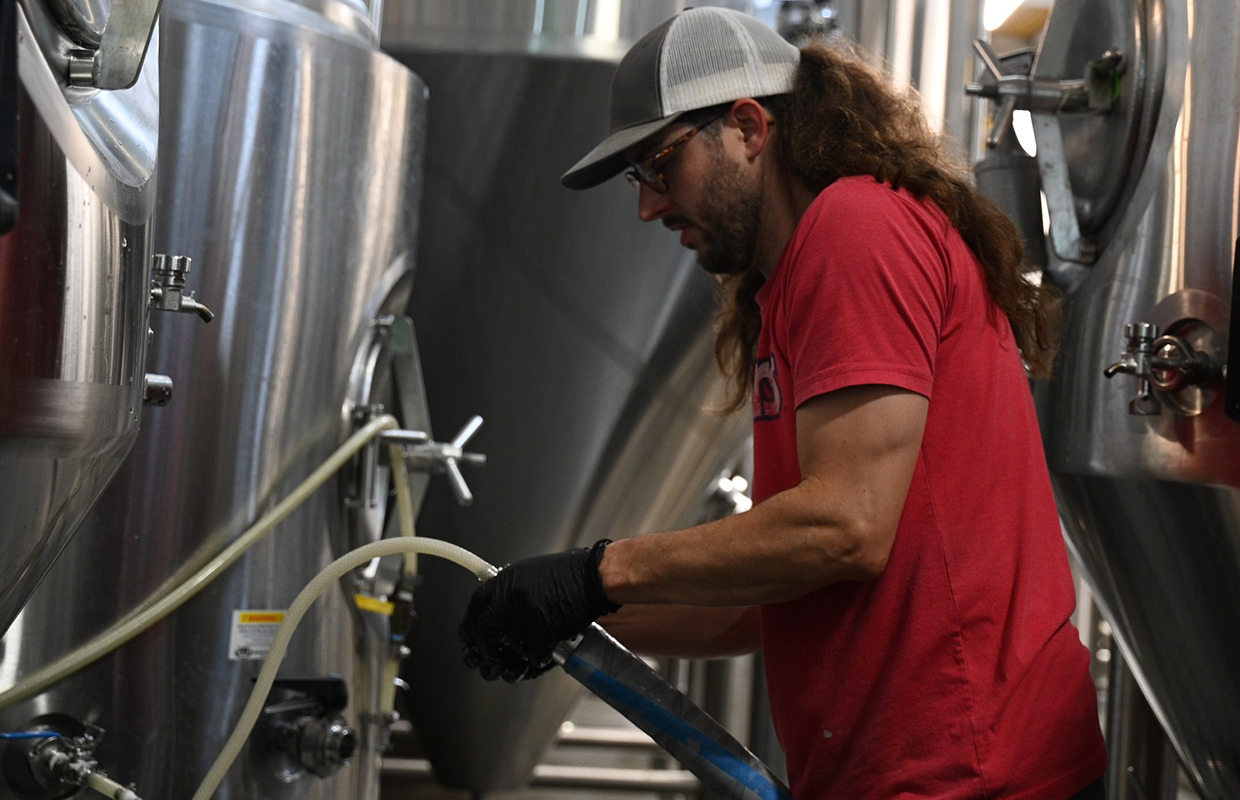
When you are told your overall co2 usage needs to be cut by more than half due to supply chain issues, you need to think fast. Fast thinking is what Dorchester Brewing has been doing for the past month or so and the Boston-area brewery shared with Brewer some quick steps they took in reducing reliance on co2 and converting production processes to nitrogen where they could.
Saying that they are not planning to be the next Guinness or a nitro-beer heavy brewery as the fix, Dorchester Director of Brewing Operations, James Haugh, explained that they knew that they needed at least an aggregate of how much co2 they use for their finished beers on a given week.
“Then we also ran some calculations to see how much co2 would keep our tap lines flowing without any disruption to service,” he said. “We’re obviously purging all of our bright tanks, carbonating our beers, and then providing co2 blankets for our canning lines and seaming machines. So we all kind of got together and figured out where we can supplement nitrogen into some of these processes.”
“If you don’t have co2, you’re not going anywhere fast, right?”
Every brewery, from startups to the biggest breweries, can be more mindful of how they’re using this finite resource, he added. So how do you pivot to keep the train on the tracks and moving forward? Here are places to look at first.
- Spunding Valves: Haugh said they have spunding capabilities for all 19 of its 60-barrel fermenters. “Pretty much right after we repitch yeast or dry hop, we start spunding our tanks to let that pressure build up. Then we’re transferring through our centrifuges under pressure. Fortunately, we’re able to send our beer into the brite tanks already at least 1.5 to even 1.8 Vols. It’s a pretty new process that we’ve implemented using balancing lines and spunding valves. So it’s another huge win.”
- Purging/Cleaning Brite Tanks: Dorchester has co2 lines that wrap around the entire brewery with multiple drop points throughout the facility that you can tap into. “If you’re a smaller brewery, and you have your co2 tank in place, it’s just whether it’s hard piped or polyline that you would essentially just swap out your gas source,” Haugh said. “Even if it’s a 350 or 750-gallon liquid nitrogen doer, we were depleting the demand more than the supply so we actually needed to bring in a vaporizer, which increases the amount of gas you can get off of a tank per hour. We use the vaporizer to get more volume out of the tank. For our brite tanks, we created another polyline that attaches right from the liquid nitrogen tank and vaporizer, to the tank.” Dorchester is also working with its chemical company to figure out the right mix of CIP vs. CUP as well.
- Canning/Seaming Lines: The canning line and seamer were all hard piped in. So Haugh said they cut those lines with the help of a fabricator and inserted stainless block and bleeds to make the conversion for gaseous nitrogen into those pieces of equipment. “We’re starting that process of doing R&D on those isolated pieces of equipment to make sure that the long-term stability is adequate and we’re not jeopardizing anything,” he said. Haugh said their Krones canning line switch was fairly easy as it is common practice, which made for a fairly straightforward swap over.
“I think everybody is going to come out better on the other side of this because they’re going to be more mindful,” Haugh said. “Nitrogen is 70% of the air we breathe. You might pay a little bit more per pound when you’re buying it, but you know that those resources aren’t going anywhere. So it’s almost worth a little bit more just to know that these processes that — I need co2 for, even if I have a smaller supply of it — I can concentrate that supply on the stuff that I can’t get away with changing the gas on.”
It was especially important to Dorchester to get things quickly done because Haugh says about 90% of the brewery’s production is for other breweries.
“When you get that type of scare, right off the get-go, you’re just thinking of your partner’s production continuing to flow and to get them their beer where they need it and when they need it,” Haugh said. “There was an extra level of putting our heads together to figure out how we can navigate and get over some of these hurdles.”
The brewery also has said they will offer up help to breweries in New England during their transition to nitrogen by using their dedicated QA/QC lab, team, and facilities to test DOs and can seams for free.
“We were thinking of ways of how we could help even though we are in the same trenches as a lot of other people, we do have some resources that could be made available,” Haugh said. “We’re just trying to do our part, it’s a big industry, but it’s also a fairly small industry.”
Be the first to comment