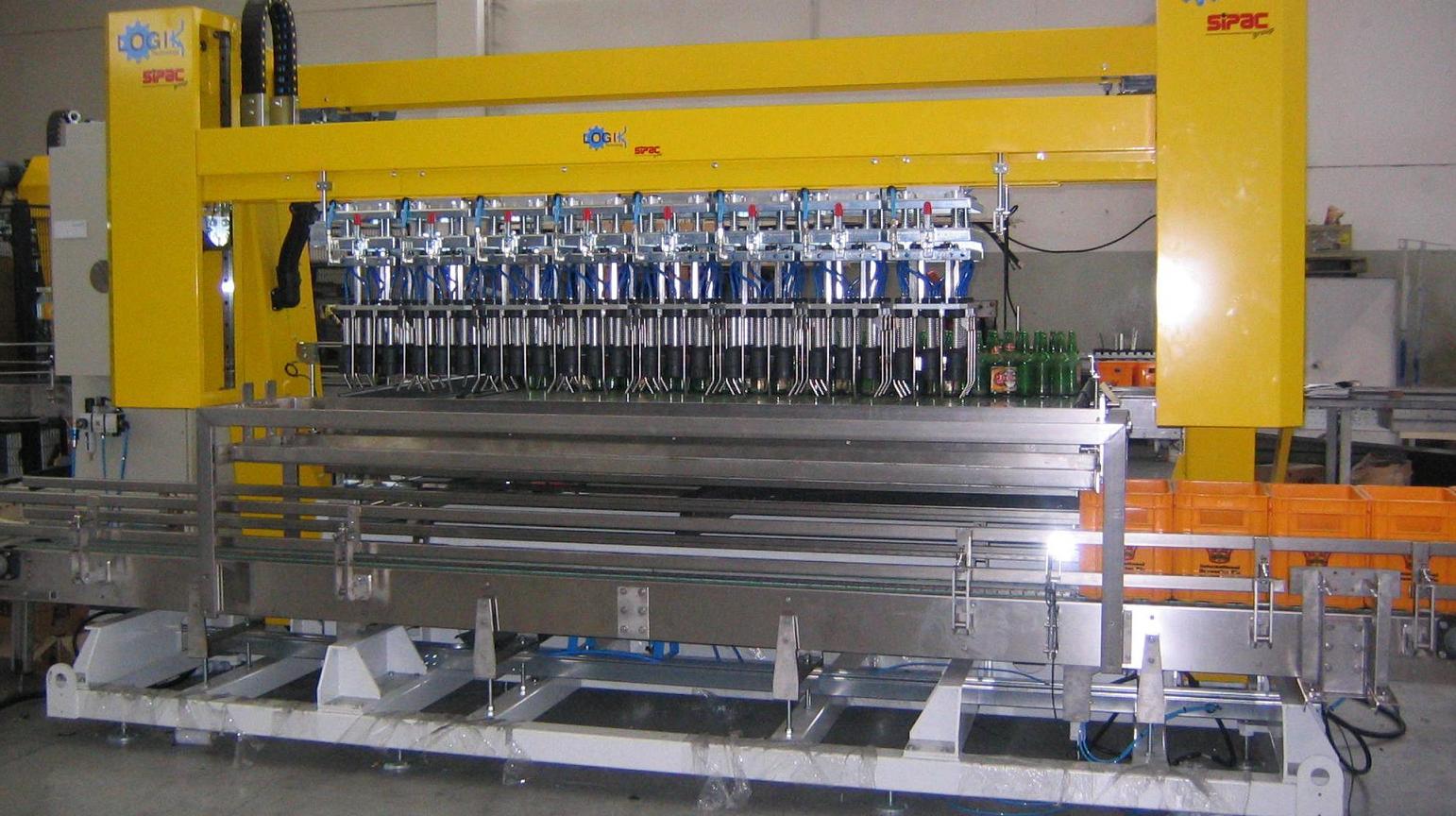
Emmeti USA, Leading the industry with the most innovative, technologically advanced factory automation equipment introduces the most diverse pick and place case packer named, “The Eagle,” designed to effectively pick and place pack a variety of case sizes and containers.
Tampa, Florida, May 6, 2015: Fausto Savazzi, President of Emmeti USA, says, “Emmeti’s case packer, with automatic job change, is capable of quickly and easily changing from one bottle size, or product to the next. The range covered by our self-adjustable head on The Eagle Case Packer is 60 to 110 mm bottle diameter, or 2.3” to 4.3”. Emmeti is a global supplier, and pick and place case packing is not a new concept to the market. Bottling lines around the world pick and place case pack, therefore this method is standard operating procedure on Emmeti Case Packers. Our case packers meet the needs of low volume to high speed lines, accommodating bottlers and repackers from the high end, top shelf labels, to a mobile bottling truck, without jeopardizing the label or integrity of the product.”
Typically from the labelers, the bottles travel through continuous bottle dividers that separate them into a number of lanes (depending on the speed) entering the case packer. Using brushless motors, the bottle dividers, designed by Emmeti, receive bottles from a single lane conveyor and divert them into separate infeed lanes traveling to the case packer area, while maintaining a single line to feed the case packer. The flow of the bottles (or containers) does not slow down or stop the conveying line. Fingerlike devices check to ensure that the bottles in the pick-up zone are positioned correctly and determine if any bottles have fallen. If a fallen bottle is detected, the system stops until correction is made. Once corrected the case packer automatically ramps back up to accommodate the lost production time.
The case packer loads from one to ten cases at a time and can insert partitions after bottle placement: After the required number of bottles / containers enters the pick-up zone, a bar holds back additional incoming bottles / containers to avoid back pressure on the bottles, during the pick-up cycle. The system is designed to eliminate any contact between bottles and guides, thus avoiding any bottle or label damage, after the pick-up. When required, partitions are inserted after placement of bottles and the partition tamps itself in place with the help of a vibrating conveyor, upon exit from the case packer zone.
The Eagle case packer can be set up to accommodate a wide range of products using gripping, magnetic or vacuum pick-up systems. A carton centering device in the case packer ensures that the carton is positioned correctly to receive the bottles while a sensor detects the presence of the carton. If a case is missing, or not properly positioned, the machine automatically stops. Additional sensors allow the machine to restart only when the right number of cartons is in position and stop the machine if a jam occurs outside of the case packer. The case packer will then “ramp up” to accommodate the lost production time in the packing area.
Be the first to comment