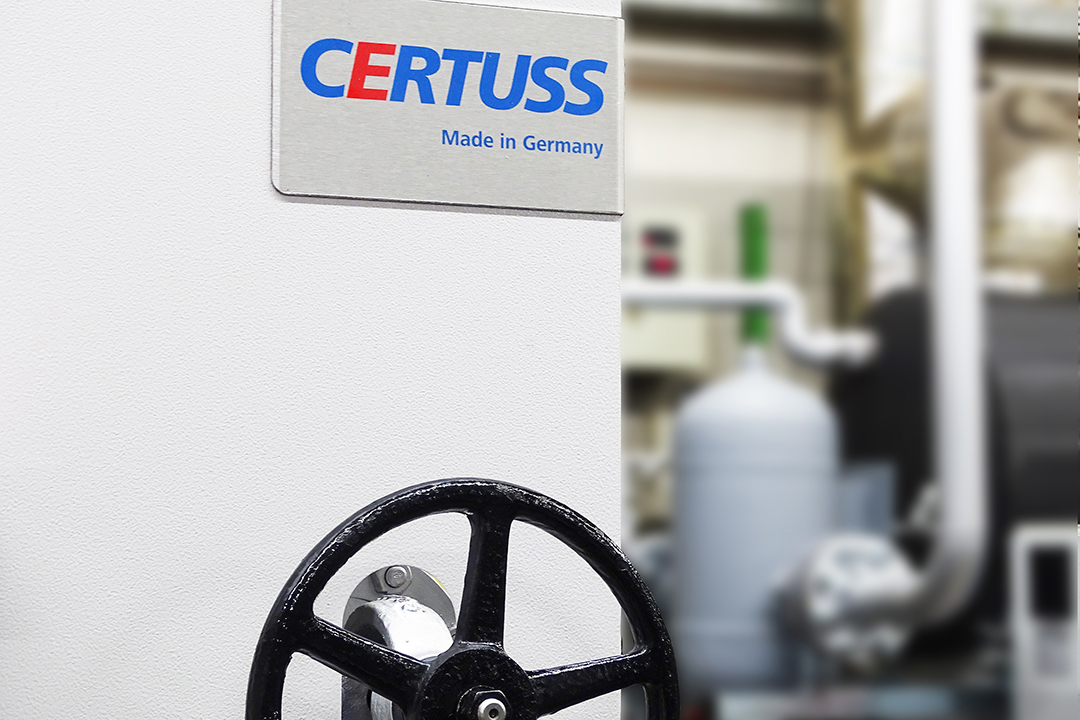
BREWER: Can you tell me the background of your company? How has your company changed since you started?
DEIMANN: CERTUSS is a company with a very long history — a 62-years’ history, to be precise. It was established in 1957 in Krefeld, Germany, aiming to manufacture reliable, low-noise and compact steam generators. We are market leaders in Germany with 60% market share and a global player operating in 130 countries and serving 89 industries. Since 2014 we are present in the US market with own subsidiary in Philadelphia and a network of 14 experienced and trained sales and service partners. Needless to say, CERTUSS has had right from the beginning its R&D Department, so we have not just followed the developments in the field, we are pioneers for a large share of them. The most recent advances are in remote monitoring of equipment.
BREWER: What are the key product features of interest for the brewing industry?
DEIMANN: The first issue is operational safety. Every so often we unfortunately still hear and read of accidents caused by steam during operation. CERTUSS uses the water tube boiler principle, needing less than 1/10th of the pressurized cooling water capacity required by a traditional firetube boiler. For us, boiler codes and standards are the minimum bar that must be reached for safe boiler design and construction. The second key product feature is that, thanks to our vertical design we can fit the tightest given space. Not only that: but our modular design allows for the maximum flexibility. Our feedwater skid can supply up to four generators, providing for N+1 redundancy with less installed BHP, peak time coverage and future capacity enlargements. A start-up time of three to five minutes, a gas-to-steam efficiency of >87% and other features such as the remote access or the BMS compatibility are huge benefits for our clients in any industry.
BREWER: What sort of clients do you work with and how do you adapt to their needs?
DEIMANN: As said we serve 89 industries and our clients are in the food and beverage sector, in the service and hospitality, in healthcare and chemical sector, in the automotive, construction and engineering, we practically have a huge experience in every industry where there is a steam application. And the reason for it is that we constantly adapt our engineering solution to the specific needs of the client, whether a new steam plant, an expansion or a retrofit. We cooperate with our local partners and the engineering firms or suppliers of brewery equipment and follow each and every project in all their steps from planning until commissioning.
BREWER: Do you have a client story to share? Something that you are excited to be a part of their success?
DEIMANN: Many! With over 14,000 boilers operating globally, we have plenty of stories to share and each project is unique. I invite you to read some of those on our website. We are particularly happy though for two of our latest craft breweries, Yards Brewing in Philadelphia and the Hardywood Craft Park Brewery in Richmond, Virginia: not just for our success, but for being part of the success of people with vision and commitment to the community.
BREWER: What are you working on right now that you think is forward-thinking and going to help boost a brewery’s growth and innovation?
DEIMANN: We’re investing much effort in the remote monitoring. We offer the possibility for remote access to our clients via mobile phone or tablet. Craft brewers don’t need to have their steam systems running 24/7. When they do need steam, they can turn on the generator from any internet-enabled device. At the same moment, we offer our clients the possibility to connect their boilers to our cloud database. We can log on, check various parameters and advise in terms of troubleshooting and maintenance. Predictive maintenance is based on data generated over years and results into cost saving and efficiency increase.
Be the first to comment